Optical Comparator (Profile Projector)
What is Wire Forming and How Does It Work?
Discover the world of wire forming and gain a clear understanding of what it is and how it works. Explore the wire forming process, learn about wire bending machines, and discover the metals that can be drawn into a wire.
What is Wire Forming?
Wire forming is the changing of the shape of a metal wire using different bending/forming processes depending on the application or use case. Although these terms are generally interchangeable, bending may only refer to one step in the process, while forming refers to the process as a whole.
How Does the Wire Forming Process Work?
The wire forming process works in four steps: wire drawing, wire straightening, wire forming, and finishing. Each of these steps is crucial for producing a finalized wire that works well with its applications. When conducting the wire forming process, there are three options: a manual wire bending machine, a computer numerical control (CNC) wire bending machine, or a four slide machine.
Step 1: Wire Drawing
Before the wire goes through the wire bending machine for forming, it needs to be drawn. Wire drawing works by pushing a wire through a die and pulling it out of the other end. As a result, the thickness of the wire, or cross-section, is reduced.
- Forging
- Wire drawing changes the shape of metal with force, this process is also known as forging. Forging does not change any characteristic of the metal except for the shape.
- Spooler
- A spooler is a tool used at the end of the wire drawing process that winds or spools wires. Some wires are spooled and then used in the final form, whereas others still go through the wire forming process.
- Coiler
- Coilers are similar to spoolers but instead of just wrapping a wire around a spool, they coil the wire into an individual coil, such as a solenoid, or around a centerpiece.
Step 2: Wire Straightening
Next in the wire forming process is wire straightening. The wire straightening process is exactly what it sounds like – a method for straightening out any defects in the wire. During straightening, disfigurements and deformities are rolled out manually or through a CNC machine. Once the wire is fully strengthened, it is then ready for wire forming.
Step 3: Wire Forming
Finally, step three is where the actual wire forming happens. There are a few processes of forming that are done with a manual or automated machine.
- Manual
- Manual wire bending machines get their name from the caveat that they require manual labor, even if they are partially automated. The manual process may be manually moving the machine, manually turning the wire, or manually adjusting throughout the procedure. With the accessibility of integrated and intelligent technology moving into the machining industry, manual wire forming is becoming outdated. This process is tedious, requires manpower, and takes exponentially longer than an automated method.
- Computer Numerical Control (CNC)
- CNC machines use a pneumatic or hydraulic method in conjunction with a computer numerical control system to form the wire. In other words, these machines utilize intelligent software for the control and movement of the machine. Since these machines work at a faster and more precise pace than manual machining, CNC wire bending machines are usually preferred over manual wire bending machines.
- Four Slide
- Four slide machines can use up to four machining processes for more efficient and cost-effective machining. Because of this factor, four slides are integral to the wire forming process because of the extra methods they can add to drawing and finishing.
- Spring Wire Forming
- Spring wire forming, also known as coil wire forming, is used for creating torsional and compression springs, as well as electrical coils. These springs and coils are wound very tightly, sometimes more than once.
- Torsional Springs
- Torsional springs are tightly wound coils with straight ends on each side. The straight ends are used for holding mechanical components in place for storing and releasing energy. These are used in items like chip clips, and door hinges.
- Compression Springs
- Compression springs compress and retract as force is added or taken away. An everyday example of compression spring is the spring in a pen or a mattress.
- Roll Wire Forming
- Roll wire forming works with flat and round shapes. This type of wire forming process needs additional finishing like hardening, rounding, and prefinishing.
- Bend Wire Forming
- Bend wire forming is the process of shaping wire into configurations after the wire is cut to the desired size. Using bend wire forming does not need extra finishing. For example, consider how a paper clip is bent into shape.
Step 4: Finishing
After forming, sometimes finishing is required for the final product. The finishing step in the wire forming process may involve one or multiple processes that affect a wire’s corrosion resistance, electrical conduction, appearance, or other qualities. Some examples of finishing processes include:
- Covering with plastic or rubber
- Cutting
- Galvanizing
- Electropolishing
- Powder coating
- Plating
- Shining
Materials Used in Wire Forming
The most common materials used in wire forming are metals.
These metals are typically formed into a wire from .5 to 6.5 mm in width.
Popular metals include:
- Aluminum
- Brass
- Copper
- Stainless steel
- Steel alloys
Wire Forming Applications Across Industries
Electrical
- Electrical wires
- Cables
- Light fittings
Aerospace
- Fasteners
- Aircraft frames
Interior Design
- Filters
- Hooks
- Racks
- Baskets
- Chairs
Medical
- Orthodontic brackets
- Syringes
- Surgery wires
- Orthodontic springs
Automotive
- Suspension systems
- Steering systems
- Gear shifters
- Door handles
Implementing Wire Forming
Whether it’s in the automotive, medical, interior design, electrical, or aerospace industry, wire forming builds the foundation for parts around us. Utilizing CNC and four slide machines are efficient methods for tackling the entire wire forming process, from drawing the wire for preparation, straightening kinks for accurate forming, forming shapes, and finishing with a last layer.
Wire Form Measuring
Looking to measure your wires in your forming process? KEYENCE offers automated optical comparators that have specialized software for measuring a wire’s outer diameter, pitch diameter, and other geometric measurements with a push of a button. Request a demo today to see how painless wire measuring can be!
Related Downloads
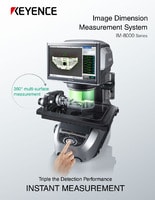
Brochure for the IM-8000 Series Image Dimension Measurement System. Accurately measure parts in seconds at the push of a button.