Optical Comparator (Profile Projector)
Extrusion
Learn about the extrusion process, explore a wide range of extruded parts, and discover the benefits of aluminum extrusion. Find the right extrusion machine for your needs and gain a clear understanding of what extrusion is and how it works.
What is Extrusion?
Extrusion is the process of forcing a material through a die’s opening to create solid, hollow, or semi-hollow extruded parts.
Consider the workings of a hand-held pasta machine. Dough is put inside of the machine, and as you crank the handle, the dough has no choice but to go through the holes and come out in pasta form. This pasta-making process is an at-home version of extrusion.
Aluminum is one of the most popular and common material used in this process. However, manufacturers also use plastic, stainless steel, copper, titanium, nickel, and various alloys.
Extrusion Process
The general extrusion process is as follows:
Extrusion Process Step 1: Die and Billet Preparation
Before extrusion occurs, the die and billet must be prepped for optimal results. The die oven is heated between 400 and 500 degrees Celsius (approximately 750 to 930 degrees Fahrenheit), and the billet is placed inside.
This temperature heats the billet enough to where it is more malleable. However, the temperature isn’t hot enough for the billet to liquefy.
Extrusion Process Step 2: Lubrication of Billet
Lubricating the billet is another part of the preparation process that ensures the extrusion process doesn’t have resistance.
During this step, a release agent is applied to the extrusion ramp. The release agent goes hand in hand with the lubrication, and the agent protects the lubricant from sticking to the ramp.
Extrusion Process Step 3: Billet Extrusion
This step is when the actual extrusion takes place for a new part. A ram adds anywhere from 100 to 15,000 tons of pressure to the billet and pushes it through the die.
As the billet comes out of the die, a puller attached to the extrusion machine will slowly start pulling the billet along the extrusion ramp to make room for more to come out.
Extrusion Process Step 4: First Cooling
After the billet comes out of the die, it is cooled by water or fans, also known as quenching, to solidify the shape.
Extrusion Process Step 5: Die Removal
Since the billet comes out of the die passage as one long part, it needs to be cut by a hot saw to remove it from the die. After removal, the billet cools to room temperature.
Extrusion Process Step 6: Shaping
The last part of the extrusion process is shaping it for its final form. In this step, the billet may be straightened and sawed.
Extruded Parts
Many everyday objects are extruded, including:
- Bleachers
- Ladders
- Pipes
- Railings
- Inspection tables
- Light fixtures
Exploring the Extrusion Process Further
Extrusion is a metal shaping method used across the architectural, automotive, electronics, aerospace, and energy industry because of its beneficial results, seamless steps, and versatility.
Benefits of the Extrusion Process
- Extrusion is an alternative to manual processes like welding
- Extrusion produces complex shapes such as rods, beams, angles, squares, rectangular tubes, and C channels.
- Scrap metal from the extrusion process may be reused.
Quality Control on Extruded Parts
Are you using extrusion in your manufacturing process and need a way to verify that your parts are in spec? Check out KEYENCE’s IM Series Instant Measurement System to see how integrating this measurement device in your project can reduce time and increase accuracy in your inspection process.
Related Downloads
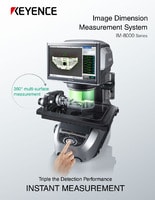
Brochure for the IM-8000 Series Image Dimension Measurement System. Accurately measure parts in seconds at the push of a button.